Simplicity and efficiency of etching
Reactive ion etching (RIE) is a type of plasma etch technology used in specialty semiconductor markets for device manufacturing.
Chemically reactive species (ions) are accelerated toward the substrate (usually a silicon wafer), to remove a specific deposited material.
A key attribute of RIE technology is its directional (usually anisotropic) etching capability.
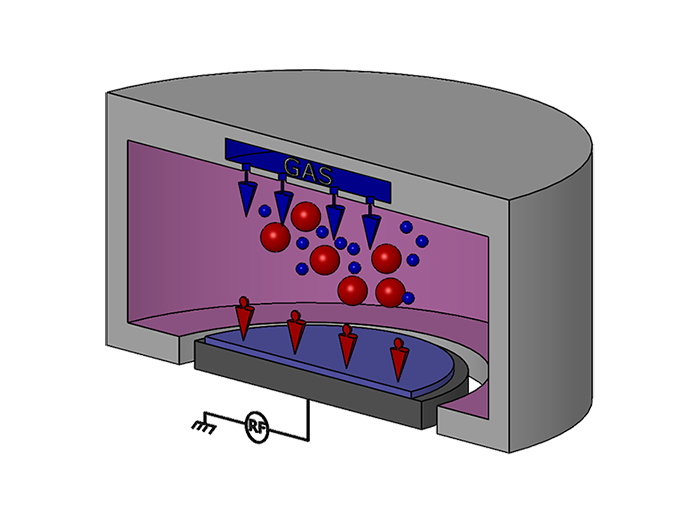
RIE technology
Plasma is initiated by applying RF power at 13.56 MHz to the powered electrode (cathode), whereas the other electrode (anode, or vacuum vessel, for example) is grounded. The electric field ionizes the gas molecules, creating the plasma.
As soon as the the discharge is ignited and plasma is established, a DC bias voltage forms on the bottom RF-powered electrode. The DC bias voltage extracts ions from the “bulk” plasma and energizes them. Thus, DC bias contributes to the directionality of etching and desorption of reaction byproducts from a wafer surface. Generation of reactive species in the bulk plasma (excited molecules, radicals, etc…) and the density of the charged species (ions and electrons) depend on the RF power applied. Because of this, the DC bias and ion current to the substrate are interdependent and are controlled with the same RF power source.
RIE equipment
Typical RIE equipment is built around a vacuum chamber with two electrodes that create an electric field which accelerates ions toward the substrate surface. Before the chamber is placed under vacuum, the substrate is transferred to the bottom (powered) electrode. Process gases enter the chamber through the showerhead in the top electrode, and the reactor is evacuated by a vacuum pump.
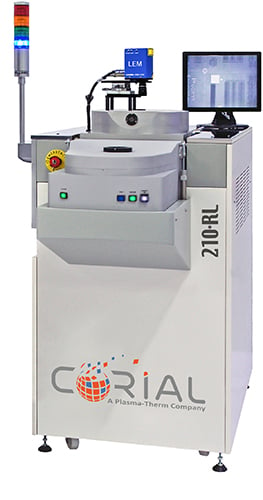
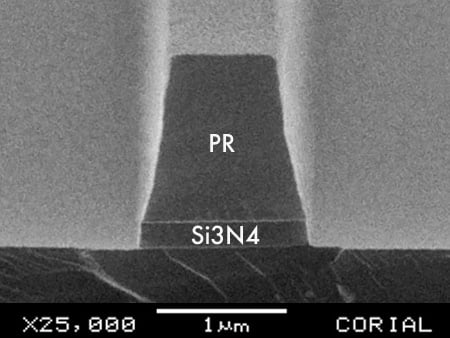
RIE processes
A wide range of materials can be etched with RIE technology
- Dielectric materials (SiO2, Si3N4, etc.)
- Silicon-based materials (Si, a-Si, poly-Si)
- III-V materials (GaAs, InP, GaN, etc.)
- Metals (Al, Cr, Ti, etc.)
Process chemistries differ depending on the types of films to be etched. Those used in dielectric etch applications are typically fluorine-based. Metal etch uses chlorine-based chemistries.
Etch conditions can be adjusted and optimized by tuning the settings of process parameters such as RF power, pressure, and gas flows. However, RIE applicability can be limited due to its relatively low etch rates.
Products
Corial 200 Series RIE Etch Systems
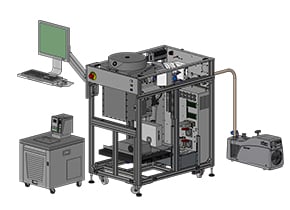
Corial 200FA
- Deprocessing of dies and packaged dies
- Fast and clean etching of SiO2, Si3N4, and polyimide layers
- Automated EPD to prevent TiN or metals etch
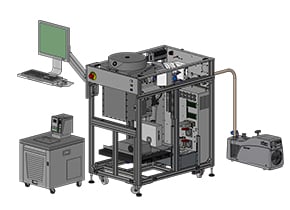
Corial 200S
- Simple to use, manually loaded RIE system
- Accepts small wafer pieces up to full 200 mm wafers
- Silicon, silicon compounds, metal and polymer etching with fluorinated gases
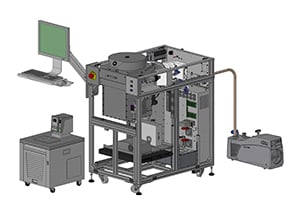
Corial 200R
- Easy-to-use system
- Module design with tiered upgrades available
- Suitable for etching silicon-based compounds, metals and polymers
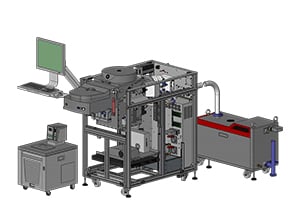
Corial 210RL
- Flexible solution for reactive ion etching
- Compatible with chlorinated chemistries
- Silicon, silicon compounds, polymers, III-V and II-VI compounds and metal etching
Corial 300 Series RIE Etch Systems
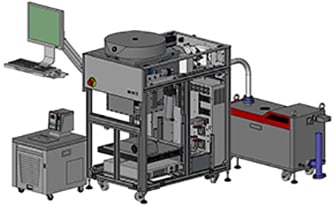
Corial 300S
- Large area reactor chromium etching for photomask fabrication
- From single wafers up to batch processing of 7 x 100 mm wafers
- Retractable liner for metal sputter etch
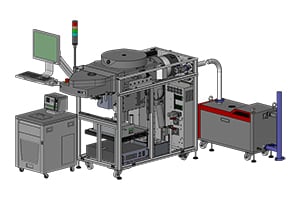
Corial 360RL
- Large area reactor chromium etching for photomask fabrication
- From single wafers up to batch processing of 7 x 100 mm wafers
- GaAs, GaP, InP, GaN and AlGaN etch