Exceptional process capability and flexibility, from damage-free processing of III-V to fast SiC etching and piezoelectric roughening
Wireless IC market overview
The Internet of Things, broadband data transfer, and more…It all becomes a reality thanks to modern wireless technologies.
The wireless market is dominated by compound semiconductor materials which are increasingly used to produce HEMTs, HBT, SAW and BAW devices.
CORIAL’s advanced dry etch technologies are capable of processing a wide range of materials used for to fabricate RF and MW active and passive devices.
CORIAL solutions
Our processing solutions offer rapid etching of SiC wafer and III-V semiconductors (GaAs, GaN) with precise shape control and low damage to the semiconductor structure. CORIAL’s products make possible the etching and surface structuring of piezoelectric materials such as lithium niobate and lithium tantalate which are widely used in SAW and BAW device fabrication.
CORIAL also delivers PECVD solutions dedicated to passivation of ICs and deposition of self-planarized dielectric coatings. Unprecedented uniformity of PECVD coatings makes CORIAL systems ideal for SAW and BAW passivation.
As device requirements continue to increase in complexity while shrinking in dimensions, Corial offers the added capability of atomic scale etching (ALE), for precise and damage-free etching of III-V semiconductor materials.
CORIAL Advantages
R
Broad application flexibility, from damage-free processing of III-V materials, to rapid etching of SiC wafer, and piezoelectric roughening
R
Clean processing with retractable liner that protect reactor, and collects etch by-products
R
One chamber for all wafer sizes
Etch processes
Wireless communication device manufacturing requires a range of etch processes, including via etch, low damage gate etch, mesa etch, and substrate etching.
Deposition processes
Wireless IC semiconductor applications require deposition of conformal interlayer dielectrics, passivation layers, and encapsulation films of various thicknesses, and on structures with different aspect ratios.
SiO2 layer with tunable stress for passivation
- Deposition rate 350 nm/min
- BOE etch rate <240 nm/min
- Stress 10 ± 50
High-quality Si3N4 film deposition
- Deposition rate 110 nm/min
- Refractive index 2.045
- Stress -100 ± 50 MPa
Products
Corial 210IL 
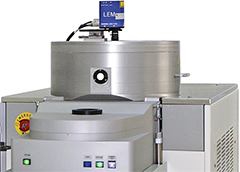
- ICP-RIE etch system with load-lock
- Fast etch rates for III-VI compounds
- Cluster configuration for integration on the Corial PS200
Corial D250 
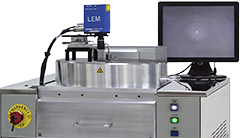
- PECVD system with in-situ plasma cleaning
- High and low-temperature PECVD
- SiO2, Si3N4, SiOCH, SiOF, and SiC films
Corial D250L 
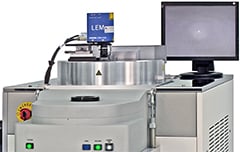
- Same capabilities as Corial D250, plus vacuum load-lock for higher throughput
Corial 360IL 
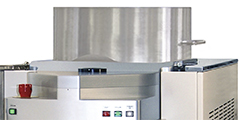
- ICP-RIE etch system for 24/7 production environment
- Load-lock for batch sizes up to 7 x 100mm wafers
- Fast etch rates for sapphire, oxides and polymers
Corial D350 
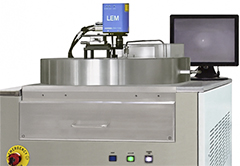
- PECVD deposition system for 24/7 production environment
- Manual loading for up to 300 mm wafers
- High quality SiO2, Si3N4, SiOCH, SiOF, SiC and aSi-H films deposition
Corial D350L 
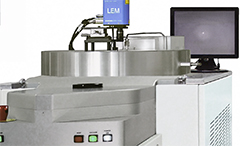
- Same capabilities as Corial D350, plus vacuum load-lock for higher throughput
Corial D500 
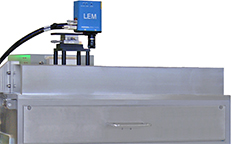
- Very large area PECVD deposition system
- High throughput: 104x2’’ ; 25x4’’ ; 9 x 6’’ or plates up to 500 mm x 500 mm