Exceptional process flexibility, from high SiC etch rates to low damage film deposition
Power devices market overview
Demand for wide bandgap power semiconductor components is principally driven by growth of the hand-held devices market, where efficient power management is appreciated key requirement.
The exponential growth in the adoption of green energy sources for industrial and consumer markets (wind power, solar cells, electric vehicles, etc.) is another driver for wide bandgap semiconductors. These materials are a critical part of high current/high voltage devices.
CORIAL solutions
Silicon carbide (SiC) and gallium nitride (GaN) are materials of choice in the manufacture of power semiconductor devices.
CORIAL offers equipment that specifically target etch and deposition processes for compound semiconductor-based power devices.
CORIAL Advantages
R
Equipment is easily scalable from R&D to volume production
R
Retractable liner protects reactor, and collects etch by-products
R
One chamber for all wafer sizes
Etch processes
Power semiconductor device manufacturing requires a range of dry etch processes, including deep trench etch, smooth feature etch, and low damage etch.
Deposition processes
Typical plasma enhanced deposition applications for power device manufacturing include passivation, dielectrics, and masks. CORIAL’s PECVD tools are designed to ensure tight control of film stress, from tensile to compressive, and to produce high deposition rates films without any compromise in uniformity or film quality. CORIAL also offers low temperature and low damages PECVD processes for nitride and oxide films.
High-quality Si3N4 film deposition
- Deposition rate 110 nm/min
- Refractive index 2.045
- Stress -100 ± 50 MPa
SiO2 layer with tunable stress for passivation
- Deposition rate 350 nm/min
- BOE etch rate <240 nm/min
- Stress 10 ± 50 MPa
Thick SiO2 film deposition for hard mask
- 100 µm thick layers
- Deposition rate 550 nm/min
- No manual cleaning required
Products
Corial 210IL 
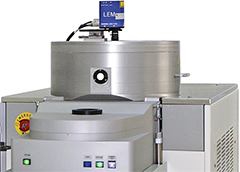
- High density ICP source for rapid etching of hard materials
- Excellent process repeatability
- Excellent particle control (liner)
Corial D250 
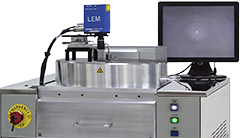
- PECVD system with in-situ plasma cleaning for high uptime
- High and low temperature PECVD
- SiO2, Si3N4, SiOCH, and SiC film deposition
Corial D250L 
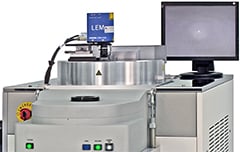
- Same capabilities as Corial D250, plus vacuum load-lock for higher throughput
Corial 360IL 
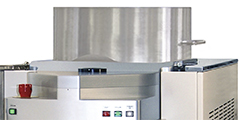
- ICP-RIE etch system for 24/7 production environment
- Batch sizes up to 7 x 100 mm wafers
- Fast GaN etch rates
Corial D350 
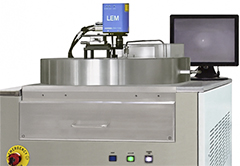
- PECVD deposition system for 24/7 production environment
- Manual loading for up to 300 mm wafers
- High quality SiO2, Si3N4 films deposition
Corial D350L 
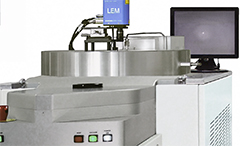
- Same capabilities as Corial D350, plus vacuum load-lock for higher throughput
Corial D500 
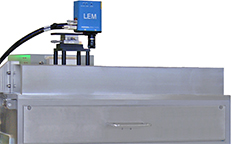
- Very large area PECVD deposition system
- High throughput: 104x2’’ ; 25x4’’ ; 9 x 6’’ or plates up to 500 mm x 500 mm