High etch rates, process flexibility and reduced ion bombardment
Inductively Coupled Plasma RIE (ICP-RIE) is an etch technology often used in specialty semiconductor markets for device manufacturing.
This technology can combine both chemical reactions and ion-induced etching. The independent control of ion flux enables high process flexibility.
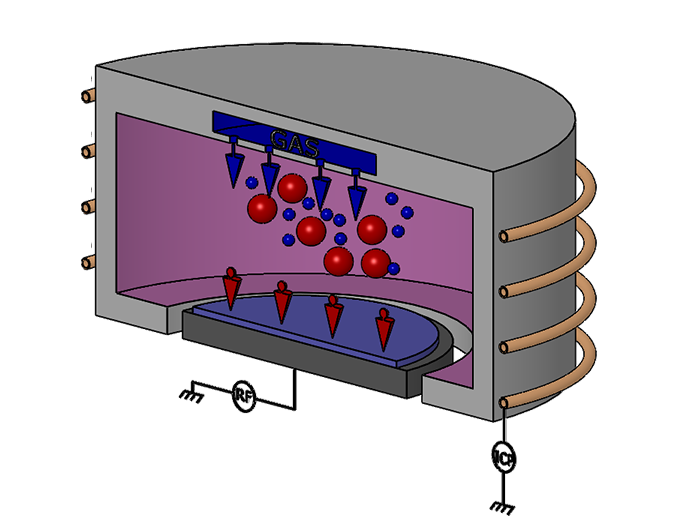
ICP-RIE technology
ICP-RIE etching is based on the use of an inductively coupled plasma source.
The ICP source generates a high-density plasma due to inductive coupling between the RF antenna and the plasma. The antenna, located in the plasma generation region, creates an alternating RF magnetic field and induces RF electric fields, which energize electrons that participate in the ionization of gas molecules and atoms at low pressure. Due to the absence of an electric field near the reactor walls there is virtually no ion bombardment or erosion of the walls.
The key differentiation between ICP RIE and RIE is the separate ICP RF power source connected to the cathode that generates DC bias and attracts ions to the wafer. Thus, with ICP RIE technology it is possible to decouple ion current and ion energy applied to the wafer, enlarging the process window.
Materials are etched with the use of a chemically reactive plasma under low pressure conditions, potentially combined with ion-induced etching.
ICP-RIE equipment
ICP-RIE tools use an Inductively Coupled Plasma source, meaning that plasma is generated with an RF powered magnetic field. By adding an inductively coupled plasma source to a standard RIE system, very high plasma density can be achieved.
Two design approaches to an ICP reactor are typically used by equipment manufacturers to produce an ICP-RIE etch system: a planar ICP source, or a cylindrical ICP source.
ICP-RIE systems typically run at low pressures and use two independent RF sources. A 2 MHz RF generator applies power to the ICP coil which controls ion fluxes, while bias power is applied to the lower electrode using a 13.56 MHz RF generator to extract and accelerate ions and radicals from the plasma towards a substrate surface. This configuration results in independent control of ion density and ion energy for higher etch rates, greater process flexibility and profile control, and reduced damage of the sample.
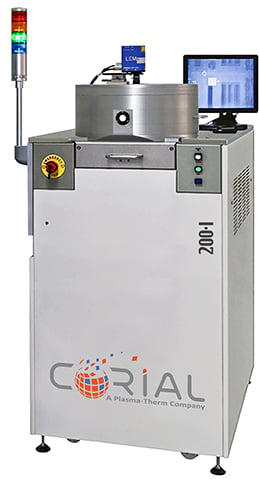
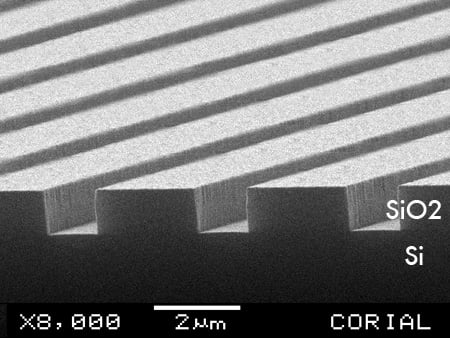
ICP-RIE processes
ICP-RIE can be used for rapid etching of a wide range of materials, including semiconductors, dielectrics, metals, and polymers. The available processes span from low damage ICP etch processes to the etching of hard materials.
Process chemistries differ depending on the types of films to be etched. Those used in dielectric etch applications are typically fluorine-based. Metal etch uses chlorine-based chemistries.
Etch conditions can be adjusted and optimized by tuning the settings of many process parameters such as RF power, pressure, and gas flows.
Products
Corial 200 Series ICP-RIE Etch Systems
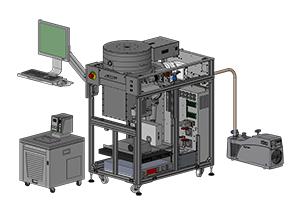
Corial 200I
- For single wafers over up to 200 mm, dies or packaged dies
- Fluorinated and oxygen based chemistries
- Silicon compounds and polymer etching
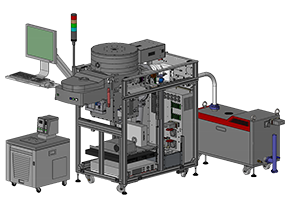
Corial 210IL
- Small wafer pieces up to full 200 mm wafers
- Supports ICP, RIE, ALE and DRIE process recipes in the same reactor
- Fast etch rates and excellent uniformities
Corial 300 Series ICP-RIE Etch Systems
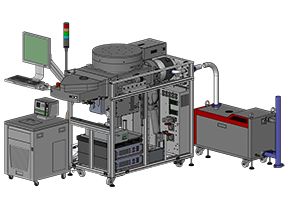
Corial 360IL
- System for 24/7 volume production environment
- Load-lock for batch sizes up to 7 x 100mm wafers
- Fast etch rates for sapphire, oxides, and polymers