Highly conformal coating for MEMS, nanotechnology applications, and semiconductor devices
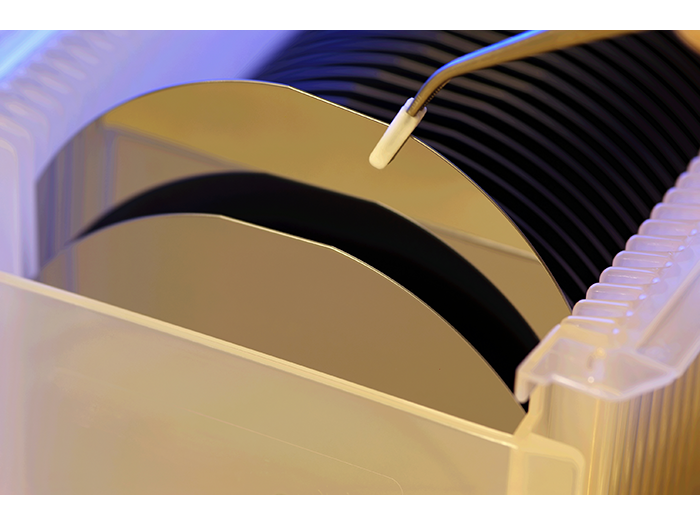
ALD technology
Atomic Layer Deposition (ALD), used to deposit films on a monolayer scale, has become widely adopted in R&D and various industries.
The ALD mechanism proceeds by a limited surface chemical reaction, and thus ALD processes offer superior deposition uniformity and conformality over varied substrate sizes and shapes.
ALD process cycle
ALD is a time-multiplexed process comprising of cycles with 4 steps in a cycle.
After completion, the ALD cycle is started again, producing layer-by-layer growth.
Precursor exposure
During step 1 of the cycle, reactive species are introduced in the reactor and chemisorbed on the wafer surface.
Purge
In process step 2, purging of the reactor is required to remove all traces of the reactant.
Reactant exposure
The second reactant is introduced into the reactor in step 3. The reactant molecules can react with the adsorbate violently upon plasma excitation (plasma enhanced ALD, or PEALD). Due to the self-limiting process, and with the proper choice of reactants and process conditions, only a thin layer, close to a monolayer in thickness, is formed during the chemical reaction.
Purge
Byproducts released are purged from the reactor during step 4.
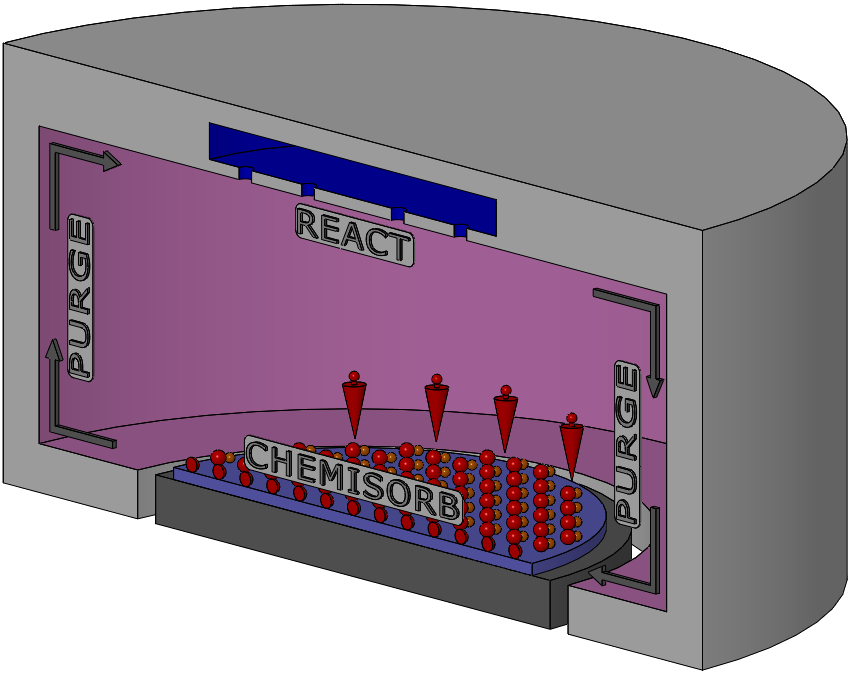
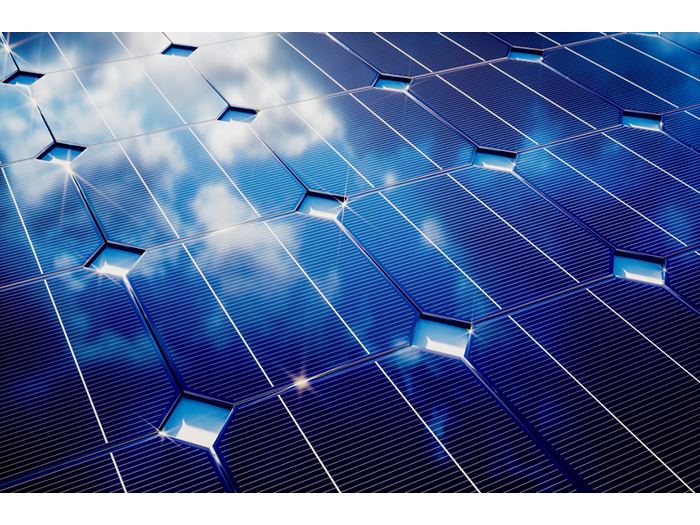
ALD processes
Continued progress has been achieved with ALD, demonstrating the capability to use this technique to deposit a variety of materials.
Products
Corial 200 Series System for Atomic Layer Deposition
Process control software for time-multiplexed processes
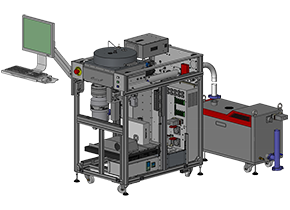
Corial D250
- Deposition system with the capability to operate in PECVD and ALD modes in the same reactor
- Plasma-enhanced ALD for higher quality films
- Handling up to 200 mm wafer sizes
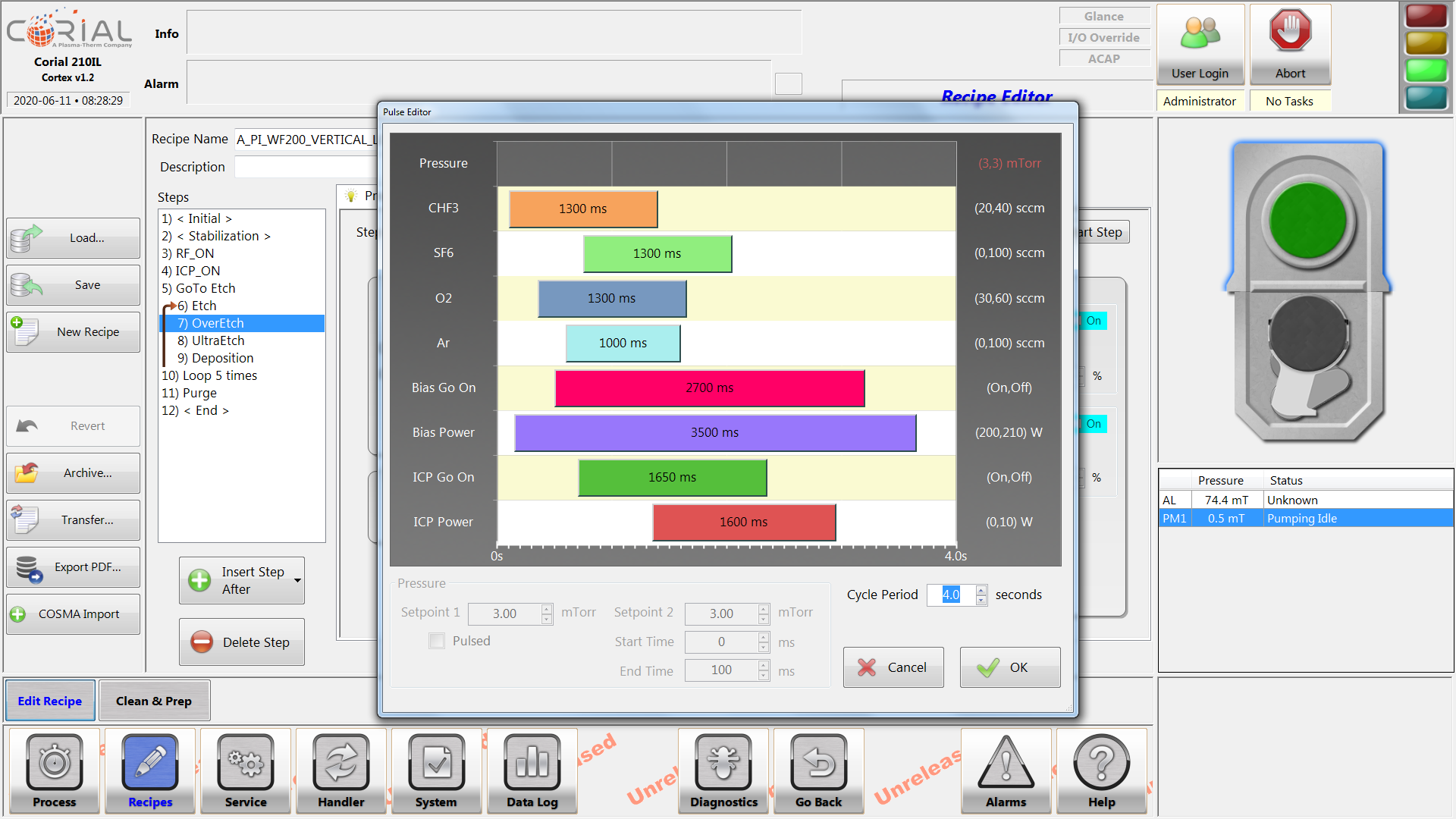
CORTEX™ Pulse
- Enables ALD process control on conventional PECVD systems
- Advanced tuning of RF pulsing to control ion energy
- Independent and rapid pulsing of gases, down to 10 ms
- Real-time process adjustment